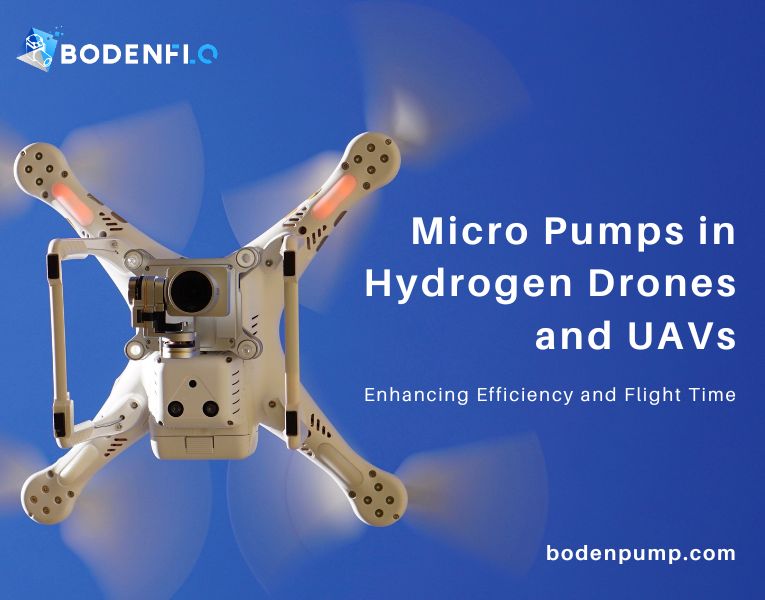
Unmanned Aerial Vehicles (UAVs) or drones are revolutionizing industries ranging from logistics and surveillance to environmental monitoring and infrastructure inspection. As demand for extended flight time, reduced carbon footprint, and higher efficiency increases, hydrogen-powered drones are emerging as a game-changing technology. However, optimizing their hydrogen fuel cell systems requires precise fluid and gas management, where micro pumps play a crucial role in ensuring consistent hydrogen delivery, cooling, and pressure regulation.
Micro pumps provide precise hydrogen circulation, coolant flow management, and pressure regulation, making them a critical component in hydrogen fuel cell drones. These lightweight, high-efficiency pumps ensure stable hydrogen delivery and optimized thermal management, allowing UAVs to achieve longer flight endurance while maintaining system efficiency.
In this article, we explore how micro pumps contribute to fuel supply, cooling, and pressure regulation in hydrogen-powered UAVs and why diaphragm micro pumps are the preferred choice for ensuring optimal drone performance.
Why Are Hydrogen Fuel Cells Ideal for UAVs?
Hydrogen fuel cells are gaining popularity in UAV applications due to their high energy density, zero-emission operation, and longer flight times compared to traditional lithium-ion batteries.
Key Advantages of Hydrogen Fuel Cells in Drones:
✔ Extended Flight Duration – Hydrogen has a much higher energy-to-weight ratio than lithium batteries, allowing drones to operate for 2-5x longer.
✔ Faster Refueling – Unlike batteries that require long recharging times, hydrogen refueling takes just minutes, enabling quicker turnaround times for continuous operations.
✔ Zero Emissions – Hydrogen fuel cells produce only water and heat, making them ideal for environmentally sensitive operations such as agriculture, surveillance, and scientific research.
✔ Higher Payload Capacity – Due to their lighter weight compared to high-capacity lithium batteries, hydrogen-powered UAVs can carry heavier payloads while maintaining efficient energy consumption.
Despite these benefits, precise hydrogen flow regulation, cooling, and pressure control are necessary to ensure UAVs operate safely and efficiently. This is where micro diaphragm pumps come into play.
How Micro Pumps Enhance Hydrogen UAV Performance
Hydrogen UAVs require precise fuel management and thermal regulation to optimize performance and reliability. Micro diaphragm pumps provide lightweight, high-efficiency solutions for key processes within hydrogen-powered drones:
1. Hydrogen Circulation and Delivery
The controlled flow of hydrogen from onboard fuel tanks to the fuel cell stack is essential for consistent energy output. Micro diaphragm pumps ensure stable hydrogen circulation, preventing fuel starvation and ensuring optimal chemical reactions within the fuel cell.
🔹 Why Micro Pumps Are Ideal for Hydrogen Supply:
✔ Precise Flow Control – Provides a consistent flow of hydrogen without pulsation, improving fuel cell efficiency.
✔ Compact & Lightweight – UAVs require minimal weight components, making micro pumps a perfect choice for hydrogen delivery.
✔ Oil-Free Operation – Prevents contamination of hydrogen, maintaining fuel cell purity and system longevity.
Technical Parameters for Hydrogen Circulation Pumps:
- Flow Rate: 0.5 - 5 L/min
- Operating Pressure: 50 - 300 kPa
- Material: PTFE, PPS (high resistance to hydrogen exposure)
2. Thermal Management and Cooling
Hydrogen fuel cells generate heat, which can degrade performance if not managed properly. Efficient cooling systems are essential to maintain optimal operating temperatures for both the fuel cell stack and electronic components.
🔹 Micro Pumps in UAV Cooling Systems:
✔ Coolant Circulation – Ensures efficient heat dissipation from the fuel cell stack, preventing overheating.
✔ Deionized Water Compatibility – Used for liquid cooling loops in advanced hydrogen fuel cell systems.
✔ Low Power Consumption – Allows maximum energy efficiency without reducing overall UAV endurance.
Technical Parameters for UAV Cooling Pumps:
- Flow Rate: 1 - 10 L/min
- Operating Pressure: 100 - 500 kPa
- Pump Material: PPS, PTFE (compatible with coolant liquids)
3. Hydrogen Tank Pressure Regulation
To maintain a stable hydrogen flow, UAVs must regulate pressure between high-pressure storage tanks and the low-pressure fuel cell stack. Micro diaphragm pumps with pressure sensing capabilities help balance pressure fluctuations, improving fuel efficiency and safety.
🔹 How Micro Pumps Assist in Pressure Regulation:
✔ Stable Gas Flow – Ensures smooth transition from high-pressure tanks to usable low-pressure hydrogen.
✔ Prevents Fuel Starvation – Maintains consistent pressure, avoiding energy fluctuations.
✔ Compact Design for UAVs – Minimizes weight while maximizing pressure control efficiency.
Technical Parameters for Pressure Regulation Pumps:
- Flow Rate: 0.3 - 5 L/min
- Pressure Range: 50 - 800 kPa
- Diaphragm Material: PTFE, FKM (resistant to hydrogen exposure)
Why Are Diaphragm Micro Pumps the Best Choice for Hydrogen UAVs?
Micro diaphragm pumps have distinct advantages over other pump technologies when it comes to hydrogen UAV applications.
Advantages of Diaphragm Micro Pumps in Hydrogen UAVs:
✔ Oil-Free Design – No risk of contamination, ensuring hydrogen fuel purity.
✔ High Chemical Resistance – PTFE diaphragms withstand exposure to hydrogen and other fuel cell byproducts.
✔ Lightweight & Compact – Optimized for drones where weight reduction is crucial.
✔ Low Power Consumption – Essential for maximizing UAV flight duration.
✔ Long Lifespan & Reliability – Brushless DC (BLDC) motor design ensures minimal maintenance.
Unlike traditional piston pumps or centrifugal pumps, diaphragm pumps operate with minimal moving parts, reducing vibration, noise, and wear—critical factors in UAV applications.
BODENFLO’s Contribution to Hydrogen UAV Technology
At BODENFLO, we specialize in high-performance micro diaphragm pumps designed for hydrogen fuel cells, UAV cooling, and precision pressure regulation. Our pumps are engineered to meet the strict requirements of lightweight, high-efficiency UAV systems, helping drone manufacturers improve flight endurance and reliability.
Why Choose BODENFLO’s Micro Pumps?
✅ Industry-Leading Innovation – Designed for next-gen hydrogen UAV applications
✅ Customizable Flow & Pressure Settings – Tailored solutions for different fuel cell designs
✅ Ultra-Lightweight Materials – PTFE & PPS construction for fuel and coolant compatibility
✅ High Energy Efficiency – Low power consumption extends UAV flight time
✅ Proven Reliability – Engineered for long-term hydrogen exposure without performance loss
As the UAV industry continues to transition towards clean energy solutions, BODENFLO remains at the forefront of micro pump technology, delivering advanced solutions for hydrogen-powered drones.
📩 Need expert consultation? Contact us at info@bodenpump.com to explore custom micro diaphragm pump solutions for your hydrogen UAV systems.
Conclusion
Hydrogen UAVs are redefining the future of unmanned aerial technology, offering longer flight times, zero emissions, and faster refueling. However, precise hydrogen management, cooling, and pressure regulation are essential for optimizing UAV performance.
By integrating BODENFLO’s micro diaphragm pumps, hydrogen drone manufacturers can achieve greater energy efficiency, extended flight endurance, and improved fuel cell performance.
Looking to enhance your hydrogen-powered UAVs with high-efficiency micro pumps? 🚀 Reach out to us today!