When it comes to micro liquid pumps, the choice of material can be a defining factor in the pump's performance, lifespan, and overall operational efficiency. Having been in the industry for several years, I can't stress enough how a misaligned material choice can have severe repercussions, including complete system breakdowns.
Critical considerations for material selection encompass the type of liquid being pumped, operational pressure and temperature ranges, chemical compatibility, and any industry-specific requirements. Opt for the right material and you'll not only optimize performance but significantly reduce maintenance costs and extend the lifespan of your pump.
So, shall we dive in? This comprehensive guide aims to shed light on the variety of micro liquid pump types, importance of material selection based on various operational needs, and crucial quality control and certification requirements. Prepare to get pumped with knowledge!
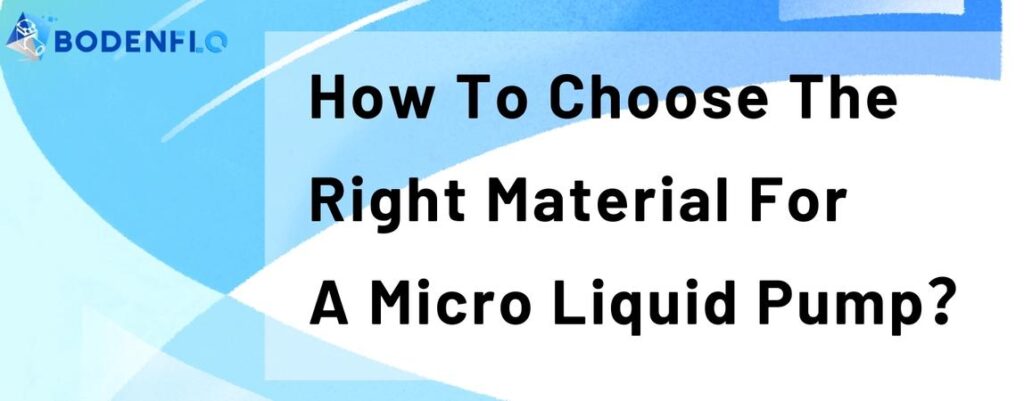
What Types of Micro Liquid Pumps Are There?
In the dynamic realm of fluid handling systems, micro liquid pumps play an essential role across a multitude of industries, from medical devices to water treatment facilities. Understanding the variety of micro liquid pump types is crucial for any procurement officer or system designer aiming to achieve optimal performance and cost-effectiveness.
Micro Diaphragm Liquid Pumps
These pumps are exceptionally versatile and find applications in medical settings, laboratory systems, and environmental monitoring. Their construction involves a diaphragm that oscillates back and forth, pushing and pulling the liquid through the pump. They offer high chemical compatibility, making them useful in systems requiring corrosive or aggressive fluids handling.
Micro Piston liquid Pumps
These are best suited for high-pressure and high-precision applications. A piston within a cylinder is actuated to create suction and discharge actions, moving the liquid. Typical applications for micro piston pumps include chromatography systems, inkjet printing, and hydraulic systems.
Micro Peristaltic Pumps
These pumps offer unparalleled sanitary capabilities, often used where sterility and cleanliness are paramount. Ideal for handling sensitive or sterile fluids like blood samples, these pumps work by compressing a flexible tubing to push liquids forward, without any contact between the pump mechanism and the liquid.
Micro Gear Pumps
These are rotary pumps that use the meshing of gears to pump fluid by displacement. They are one of the most common types of pumps for hydraulic fluid power applications. These pumps are typically used in applications where a consistent flow rate is required, such as chemical dosing and water treatment.
Importance of Material Selection
Selecting the appropriate material for a micro liquid pump is not merely a checkbox item on a procurement list. Instead, it's a critical decision that has far-reaching implications for the performance, durability, and overall cost-effectiveness of the entire fluid handling system.
Chemical Compatibility
A wrong material selection can lead to corrosion, erosion, or chemical reactions with the fluids being pumped. Such outcomes are not just expensive but potentially dangerous, especially in settings like medical laboratories, pharmaceuticals, or chemical processing plants. Therefore, understanding the chemical compatibility of the pump materials with the fluids involved is paramount.
Mechanical Integrity
Certain applications might involve high pressures or vacuums, necessitating materials that can withstand such conditions without deforming or breaking. Industrial-grade metals and special polymers are often employed in such settings to ensure mechanical integrity and a longer operational life.
Temperature Resilience
Various applications might require the pump to operate in extreme temperature conditions, either hot or cold. The selected material must be able to perform consistently across the temperature spectrum the pump will be exposed to. Failure to do so could result in material degradation, altered performance, and even system failure.
Cost Considerations
High-quality materials like special alloys or corrosion-resistant plastics can escalate costs. However, the initial investment often justifies itself by reducing maintenance costs and extending the lifespan of the pump.
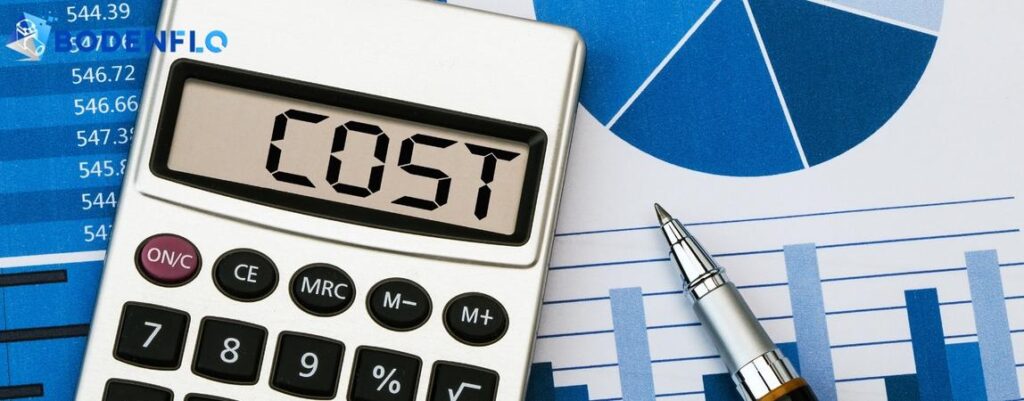
Regulatory Compliance
Certain industries have stringent regulations concerning material composition, especially when human health or environmental factors are concerned. Failing to comply can result in hefty fines, legal complications, or even the shutting down of operations.
In summary, material selection is a complex yet crucial process that combines engineering, chemistry, and economics. It's not just about "building a pump"; it's about constructing a reliable, effective, and safe mechanism integral to your operations.
Types of Materials
The choice of material for a micro liquid pump can substantially impact its performance and longevity. With a wide range of options available, it's essential to consider the specific requirements of your application when making your selection.
Metals
Stainless Steel
Widely used for its resistance to corrosion and high temperatures, stainless steel is often the go-to material for industrial and medical applications.
Aluminum
Lighter than stainless steel but equally durable, aluminum is often used where weight considerations are crucial.
Polymers
Polyvinyl Chloride (PVC)
Popular in water treatment and chemical processing, PVC offers excellent resistance to acids and bases but is generally not suitable for organic solvents.
Polypropylene (PP)
Another commonly used polymer, PP is known for its toughness, chemical resistance, and affordability.
Elastomers
Nitrile (Buna-N)
This material is an excellent choice for pumps handling oil-based substances. It offers a good balance of chemical resistance and flexibility.
PTFE (Polytetrafluoroethylene)
PTFE is a high-performance elastomer known for its chemical inertness and excellent temperature resistance. It is particularly useful in applications requiring resistance to aggressive chemicals, acids, and solvents. Furthermore, PTFE exhibits low friction, which makes it ideal for use in high-speed environments where heat dissipation is crucial.
EPDM
EPDM is primarily used in water-based or oxidative applications. They offer good heat, ozone, and weather resistance but are not suitable for applications involving oils and solvents.
Viton
Known for its resistance to a broad range of chemicals, Viton is often used in high-temperature applications and where chemical compatibility is a concern.
Each of these elastomers has its strengths and weaknesses. Hence, the material selection should be based on an in-depth analysis of the application's requirements, including factors like chemical compatibility, operating pressures, and temperatures.
Choosing the right elastomer not only enhances the efficiency and reliability of your micro liquid pump but also plays a crucial role in reducing maintenance costs and improving lifespan.
Ceramics
In specialized applications where even metals and polymers might corrode, ceramics offer a durable, albeit expensive, alternative.
Composites
Composite materials, made from a combination of different substances, can offer the best properties of several materials. They are usually custom-designed for specialized applications.
Chemical Compatibility
Chemical compatibility is a vital factor that can't be overlooked when selecting materials for a micro liquid pump. A mismatch here could lead to component corrosion, premature wear, and ultimately, pump failure. More importantly, incompatible materials could result in chemical reactions that could be hazardous to the environment or end-users.
The Role of pH Levels
Substances with extreme pH levels, whether acidic or alkaline, can be particularly corrosive. Materials like stainless steel or specialized polymers are often recommended for handling these kinds of fluids.
Organic Solvents
Organic solvents can dissolve some materials, rendering them unfit for use in a pump. In such cases, you may want to look at materials like Viton and PTFE (polytetrafluoroethylene) that offer high resistance to solvents.
Temperature Range
Different chemicals can become more aggressive or alter their properties at specific temperatures. This can also affect the material's resistance, so it's essential to consider the operating temperature when looking at chemical compatibility.
Regulatory Compliance
Chemicals used in pharmaceuticals, food, and beverage applications often require materials that meet specific compliance standards, like FDA or NSF, to ensure that no harmful substances leach into the product.
Material Testing
Whenever possible, a compatibility test should be conducted to ensure that the material of the pump is indeed suitable for the intended application. Manufacturers often provide chemical resistance charts or compatibility guides, but there's no substitute for real-world testing.
Quality Control and Specifications
When it comes to choosing a micro liquid pump, quality control and specifications are of paramount importance. A pump that fails to meet quality standards will not only affect operational efficiency but may also compromise safety.

ISO Certifications
One of the most straightforward ways to assess a pump's quality is by checking if it complies with ISO standards. An ISO 9001 certification, for instance, is a clear indicator of a manufacturer's commitment to quality management systems.
Material Certifications
Material certifications like FDA approval for food and pharmaceutical applications or NSF certification for water applications ensure that the materials used are safe and of high quality.
Precision and Tolerance
When dealing with micro liquid pumps, even minute imperfections can lead to significant performance issues. Pumps must be built to exacting tolerances to ensure optimal efficiency and lifespan.
Pump Testing
Every pump should undergo rigorous testing under various conditions to ensure that it meets all operational specifications. Tests often include those for flow rate, head pressure, and leak resistance.
Vendor Audits
Conducting an audit of your supplier can offer a deeper insight into their quality control practices. You can either visit the factory or request third-party quality control reports to gauge their level of commitment to quality.
Documentation
Detailed documentation should be available for each pump, including user manuals, installation guides, and maintenance schedules. Proper documentation aids in resolving issues more efficiently, saving time and resources in the long run.
Typical Applications and Material Selection
In various industries, the application of micro liquid pumps has proven invaluable. However, choosing the right material for these pumps is essential to meet specific operational demands.

Medical Devices
Micro liquid pumps are commonly used in medical devices such as dialysis machines and infusion pumps. In such applications, biocompatible materials like medical-grade silicone or polypropylene are often preferred to prevent adverse reactions with medications or bodily fluids.
Food and Beverage Industry
In the food and beverage sector, pumps may be involved in transferring viscous liquids like syrups or oils. Materials meeting food-grade certifications, often stainless steel or food-safe plastics, are a must.

Chemical Processing
In chemical processing, the pumps often handle aggressive or corrosive liquids. In such cases, robust materials like PTFE or PVDF are usually employed, ensuring that the pump can withstand aggressive chemicals without degradation.
Water Treatment
For water treatment applications, the focus is often on materials that are resistant to scale buildup and corrosive elements found in water, such as chlorides. Materials like ceramics or certain plastic composites are common choices.
Inkjet Printers

Inkjet printers necessitate micro liquid pumps that can accurately and efficiently pump ink through tiny nozzles. The pumps have to withstand the chemical properties of the ink, which may include solvents and pigments. Typically, materials like PTFE (Polytetrafluoroethylene) and PVDF (Polyvinylidene Fluoride) are preferred due to their excellent chemical resistance and long operational life.
Material Compatibility
It’s not just about the liquid being pumped; you must also consider the conditions under which the pump will operate. Will it be subjected to extreme temperatures? Are there any abrasive particles in the fluid? These questions are vital in selecting the right material.
Conclusion
Selecting the right material for your micro liquid pump is not merely a matter of preference, but a critical operational decision. The material must align with the specific needs of the application, whether it's medical devices, food and beverage production, chemical processing, or water treatment. A well-chosen material not only ensures efficient and safe operations but also optimizes cost and longevity. When in doubt, always consult with experts or rely on trusted vendors like BODENFLO to guide you through the complexities of material selection.