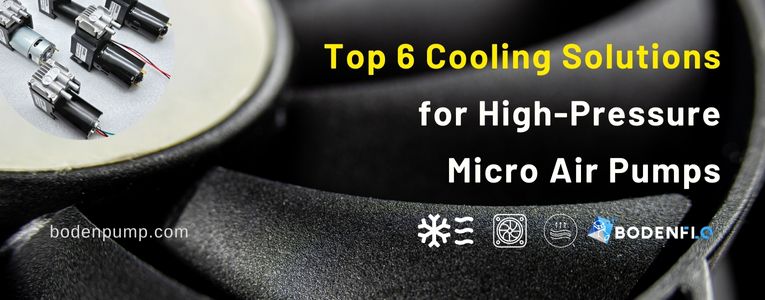
High-pressure micro air pumps are critical in various industries such as medical and automotive. The integration of these pumps in compact devices, particularly when used continuously or frequently, leads to significant heat accumulation. This heat buildup can lead to downtimes, clogging, and degradation in performance, particularly in high-speed pumps that deliver high pressure and flow rates. Effective cooling solutions are essential to prevent these issues and ensure optimal operation.
In this article, I will discuss the top 6 cooling solutions that help maintain thermal regulation for high-pressure micro air pumps, ensuring their efficiency and longevity.
1. Natural Convection
Natural convection (a basic yet effective cooling method) is the simplest and most fundamental form of heat dissipation, relying on the natural movement of air to transfer heat from the pump surface to the surrounding environment. The concept is straightforward: hot air rises and cooler air takes its place, leading to a natural airflow that helps cool the pump.
Natural convection is best suited for applications that do not require continuous operation under high loads. By incorporating design elements like fins and optimizing the surface area of the pump, manufacturers can enhance the efficiency of natural convection.
Applications of Natural Convection
This type of cooling is typically applied in environments where space is constrained, and additional components like fans cannot be accommodated. It is often used in consumer electronics and low-power medical devices where passive cooling is sufficient to maintain operational temperatures. Its simplicity makes it a cost-effective choice, but it lacks the efficiency needed for high-performance applications.
2. Forced-Air Cooling
Forced-air cooling (enhanced heat dissipation using fans) takes natural convection a step further by using fans or blowers to actively push air across the pump housing, thereby enhancing the rate of heat dissipation. This is an effective solution for pumps operating in higher power settings where natural convection alone is inadequate.
How Forced-Air Cooling Works
By utilizing a fan or blower, forced-air cooling directs air across the pump’s surface, significantly increasing heat transfer. This method is particularly effective in situations where maintaining a lower temperature is crucial to ensure pump longevity and efficiency.
Industrial Use Cases
Forced-air cooling is predominantly used in industrial automation, where high-pressure micro air pumps are required to run continuously, often under demanding conditions. Medical applications, such as ventilators, also rely on forced-air cooling to ensure that the pump remains cool, maintaining stable airflow and pressure.
3. Heat Sinks
Heat sinks are passive devices made of high thermal conductivity materials such as aluminum or copper, dHeat sinks (passive cooling devices made of high thermal conductivity materials) are passive devices made of high thermal conductivity materials such as aluminum or copper, designed to draw heat away from the pump and disperse it into the ambient environment. They are widely used in combination with other cooling solutions, providing an additional layer of thermal regulation.
Materials Used for Heat Sinks
Copper is often favored due to its high thermal conductivity, but aluminum offers a lightweight and more economical alternative. The choice of material is dictated by the specific requirements of the application, such as weight constraints or cost considerations.
Integration with Other Cooling Solutions
Heat sinks are frequently paired with forced-air cooling to optimize thermal regulation. By combining passive and active cooling elements, the overall effectiveness of heat dissipation is significantly increased, allowing for better control of the pump’s operating temperature.
4. Thermoelectric Cooling (Peltier Modules)
Thermoelectric cooling (using Peltier modules for precision), commonly achieved using Peltier modules, is a highly effective technology for situations requiring precise temperature control. A Peltier module creates a temperature gradient by passing an electric current through its junctions, leading to heat transfer from one side to the other.
Applications in Sensitive Equipment
Thermoelectric cooling is particularly advantageous in sensitive applications, such as laboratory and medical equipment, where temperature stability is essential. By using a Peltier module, it is possible to cool the micro pump to a specific temperature, thus ensuring consistent operation.
Advantages Over Conventional Cooling
Unlike forced-air or liquid cooling, thermoelectric cooling does not require moving parts, which reduces wear and tear and minimizes noise. However, its higher energy consumption and cost make it less suitable for applications that do not demand precise temperature regulation.
5. Liquid Cooling
Liquid cooling (circulating liquid coolant for maximum heat transfer) is a highly efficient means of dissipating heat, especially suitable for high-power or continuous-duty applications. The principle behind liquid cooling involves circulating a coolant through channels around the pump, effectively transferring heat away.
Components of a Liquid Cooling System
A liquid cooling system generally consists of a coolant pump, heat exchanger, and tubing that carries the coolant. The heat exchanger, often a radiator, dissipates the absorbed heat into the environment, thereby maintaining the pump at an optimal temperature.
Efficiency in High-Heat Scenarios
In high-pressure applications, where pumps generate substantial heat, liquid cooling ensures consistent temperature regulation. This method provides superior performance compared to air cooling and is thus commonly employed in industrial and high-performance computing environments.
6. Phase Change Cooling
Phase change cooling (using phase change materials to absorb heat effectively) uses materials known as Phase Change Materials (PCMs) to manage thermal loads. When these materials change from one state to another—typically from solid to liquid—they absorb large amounts of heat, making them ideal for thermal management.
Utilization of Phase Change Materials (PCMs)
PCMs are integrated into the housing or components surrounding the pump, providing a compact and effective method to absorb heat spikes. These materials are ideal for maintaining a stable operating temperature without requiring active components like fans or pumps.
Best Use Cases for Phase Change Cooling
Phase change cooling is best suited for intermittent operation applications where periods of high activity are followed by downtime, allowing the material to solidify and prepare for the next cycle. It is particularly effective in portable medical devices and emergency response equipment.
Comparative Analysis of Micro Air Pump Cooling Solutions
Efficiency
Liquid cooling offers the highest efficiency for high-power applications, while natural convection provides sufficient cooling for low-power scenarios. Forced-air and thermoelectric cooling strike a balance between efficiency and complexity.
Complexity
Natural convection is the simplest method, whereas liquid and thermoelectric cooling require more components and intricate designs, which increases the overall system complexity.
Cost Considerations
Natural convection and heat sinks are the most economical choices, while thermoelectric and liquid cooling tend to be more costly due to their components and energy requirements.
Factors to Consider When Choosing a Pump Cooling Solution
Power Consumption
The power demands of the cooling system must align with the application requirements. Passive solutions like heat sinks consume no power, while thermoelectric and forced-air cooling require a power source.
Application Environment
Environmental conditions, such as ambient temperature and airflow, play a significant role in determining the appropriate cooling solution. Forced-air cooling may be ineffective in dust-prone environments, whereas liquid cooling could be optimal.
Space and Design Constraints
Compact applications benefit from solutions like phase change materials, while larger systems can accommodate heat sinks or forced-air cooling systems.
Conclusion
Effective heat dissipation is essential to ensure the performance and longevity of high-pressure micro air pumps. Whether you opt for natural convection, forced-air, heat sinks, thermoelectric cooling, liquid cooling, or phase change materials, each solution has its advantages and limitations. Understanding your specific application needs will help you select the optimal cooling technology, guaranteeing reliable and efficient pump operation.
With 15 years of experience in manufacturing high-pressure micro air pumps, BODENFLO offers tailored cooling solutions and expert advice. Contact us (info@bodenpump.com) today to discuss your needs.