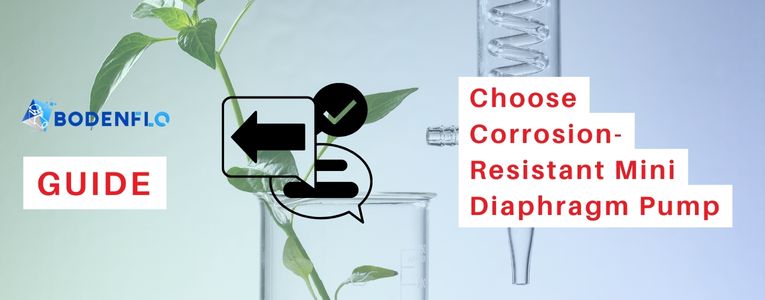
When dealing with corrosive chemicals, choosing the wrong diaphragm pump can lead to system failure, reduced efficiency, and costly repairs. Whether handling acidic or alkaline solutions, the wrong material choice can cause corrosion, leaks, and premature pump failure. In this guide, we will walk you through selecting the right diaphragm pump for your application, focusing on material compatibility, flow rate, temperature resistance, and durability in harsh environments.
To ensure reliable performance and longevity when handling corrosive media, selecting the right corrosion-resistant miniature diaphragm pump is crucial. By understanding the compatibility between diaphragm materials such as EPDM, FKM, and PTFE, as well as pump shell materials like Nylon, POM, PPS, aluminum alloy, and stainless steel, you can choose the best pump for your needs. The key to selecting the right diaphragm pump lies in understanding how different materials react to specific chemicals and operating conditions.
This article will help you make the right choice by explaining the material properties, flow rate considerations, temperature limits, and more.
Why Choose Corrosion-Resistant Miniature Diaphragm Pumps?
Miniature diaphragm pumps are often used for precise fluid transfer, providing excellent performance in chemical liquid transport across a wide range of industries. Whether you are dealing with corrosive chemicals or extreme conditions, these pumps offer several advantages:
- Compact Design: Miniature diaphragm pumps are small and lightweight, making them ideal for applications where space is limited.
- Chemical Compatibility: High-quality diaphragm pumps are specifically engineered for use with aggressive chemicals, including strong acids and bases.
- No Lubrication Required: Many diaphragm pumps are oil-free, which minimizes the risk of contamination.
- Longer Service Life: Using corrosion-resistant materials ensures longer-lasting performance, even when exposed to harsh media.
When dealing with chemical liquid transport, corrosion resistance becomes paramount. The performance of the pump will depend heavily on the materials used for both the diaphragm and the pump casing.
Key Factors to Consider When Choosing a Corrosion-Resistant Miniature Diaphragm Pump
1. Chemical Compatibility
The primary concern when selecting a miniature diaphragm pump is its compatibility with the specific acidic or alkaline medium. Different materials exhibit varying degrees of resistance to different chemicals, making it essential to choose materials that are resistant to the specific chemicals being handled.
Common materials for diaphragms include:
- EPDM (Ethylene Propylene Diene Monomer): Known for excellent flexibility, high heat resistance, and durability in water-based alkaline solutions. However, it does not work well with strong acids or solvents.
- FKM (Fluoroelastomer): Ideal for hydrocarbons, oils, and acids like sulfuric acid, but not suitable for alkaline environments.
- PTFE (Polytetrafluoroethylene): Known for its exceptional resistance to almost all chemicals, including strong acids, bases, and solvents. PTFE is often the go-to choice for handling aggressive chemicals and solvents.
The choice of shell materials is equally critical. Common materials used in diaphragms and pump shells are:
- Nylon: Affordable but less resistant to aggressive chemicals, especially acids.
- POM (Polyoxymethylene): Offers high strength and rigidity, making it suitable for applications with neutral and mildly alkaline solutions.
- PPS (Polyphenylene Sulfide): Highly resistant to both acids and bases, making it an excellent choice for strong chemical resistance applications.
- Aluminum Alloy: Used when weight is a concern but does not perform well in highly corrosive environments.
- Stainless Steel: A versatile material that provides good corrosion resistance and is commonly used in industries dealing with a variety of chemical media.
2. Flow Rate and Pressure Requirements
When selecting a diaphragm pump for chemical liquid transport, the flow rate and pressure requirements must be accurately determined. Miniature diaphragm pumps can handle flow rates anywhere from 0.3 L/min to 60 L/min, depending on the model. It is essential to choose a pump that can meet the required flow rate and pressure without sacrificing efficiency or longevity.
For example, if your application requires high pressure, stainless steel or PPS shells with PTFE diaphragms would be the most suitable choice. These materials can withstand higher pressures and harsh chemical environments.
3. Temperature Resistance
The temperature at which the pump operates can also influence the material selection. For instance:
- PTFE diaphragms can withstand higher temperatures, often up to 200°C, making them suitable for high-temperature chemical applications.
- EPDM diaphragms are generally limited to lower temperatures and are best used in moderate conditions.
- FKM diaphragms are suitable for temperatures up to 200°C, similar to PTFE, but are more commonly used in hydrocarbon and acidic media.
Temperature Resistance Comparison Table
Material | Applicable Range | Temperature Range | Remarks |
---|---|---|---|
EPDM Diaphragm | Neutral, Alkaline Liquids | -20°C to 120°C | Good for water-based and alkaline liquids, not suitable for strong acids. |
FKM Diaphragm | Acidic, Oil-Based Liquids | -20°C to 200°C | Excellent resistance to acids and oils but not suitable for strong alkalis. |
PTFE Diaphragm | Strong Acids, Strong Alkalis, Organic Solvents | -40°C to 200°C | Best for extreme chemicals and high temperatures. |
Nylon Shell | Neutral Liquids | -40°C to 80°C | Suitable for mild chemical media but not high temperatures or strong acids/bases. |
POM Shell | Neutral, Weak Acid/Alkaline Liquids | -40°C to 100°C | Suitable for mild solutions but not high temperatures. |
PPS Shell | Strong Acids, Strong Alkalis | -40°C to 200°C | Excellent for extreme chemical environments with high temperatures. |
Aluminum Alloy Shell | Neutral, Mildly Corrosive Liquids | -20°C to 120°C | Lightweight, suitable for mild corrosive liquids, limited temperature resistance. |
Stainless Steel Shell | Acidic, Alkaline Liquids | -40°C to 180°C | High strength, suitable for various chemicals but limited against strong acids and alkalis. |
When considering temperature resistance, it’s essential to select a diaphragm and casing material that can maintain integrity under the expected conditions.
4. Durability and Service Life
Corrosion-resistant materials not only ensure reliable operation in harsh conditions, but they also significantly extend the pump’s service life. PTFE diaphragms paired with PPS or stainless steel casings are the most durable for extreme chemical applications, reducing the need for frequent replacements or maintenance.
Acid and Alkali Media Compatibility Cross-Reference Table
To help you make an informed decision on which materials to choose for your miniature diaphragm pump, here is a compatibility table that matches common acid and alkali media with the appropriate diaphragm and pump shell materials.
Chemical Media | EPDM Diaphragm | FKM Diaphragm | PTFE Diaphragm | Nylon Shell | POM Shell | PPS Shell | Aluminum Shell | Stainless Steel Shell |
---|---|---|---|---|---|---|---|---|
Concentrated Sulfuric Acid | Good | Poor | Excellent | Poor | Poor | Excellent | Not Recommended | Good |
Hydrochloric Acid | Good | Poor | Excellent | Fair | Fair | Good | Not Recommended | Good |
Hydrofluoric Acid | Poor | Poor | Excellent | Not Recommended | Not Recommended | Fair | Not Recommended | Not Recommended |
Ammonia | Good | Excellent | Excellent | Good | Good | Good | Good | Good |
Sodium Hydroxide | Good | Fair | Excellent | Fair | Fair | Good | Not Recommended | Good |
Sodium Hypochlorite | Good | Excellent | Excellent | Good | Good | Good | Not Recommended | Good |
Methanol | Fair | Good | Excellent | Good | Good | Good | Good | Good |
Comparison of EPDM, FKM, and PTFE Diaphragms
EPDM Diaphragm
EPDM is a synthetic rubber that is known for its high resistance to oxidation, ozone, and weathering. It is particularly suitable for use with alkaline solutions and water-based applications, though it is not as effective with strong acids or solvents.
- Advantages:
- Good for alkaline and water-based solutions.
- Offers a long lifespan and excellent flexibility.
- Disadvantages:
- Poor resistance to acids, alcohols, and hydrocarbons.
FKM Diaphragm
FKM (also known as Viton®) is a fluorocarbon elastomer renowned for its resistance to chemicals and high temperatures. FKM diaphragms are often used in applications that involve hydrocarbons, oils, and acids.
- Advantages:
- Excellent resistance to acids and oils.
- High-temperature resistance up to 200°C.
- Disadvantages:
- Not suitable for alkaline solutions.
PTFE Diaphragm
PTFE (Polytetrafluoroethylene) is a fluoropolymer with exceptional chemical resistance. It is often used for the most aggressive chemicals, including strong acids, bases, and solvents.
- Advantages:
- Universal compatibility with most chemicals, including strong acids and alkalis.
- Excellent resistance to high temperatures and abrasion.
- Disadvantages:
- Higher cost and lower flexibility compared to EPDM and FKM.
Choosing the Right Shell Material
The shell material of a diaphragm pump also plays a critical role in determining the pump's overall performance, especially when dealing with corrosive media. Here's a quick comparison:
- Nylon: Ideal for low-cost applications but not suitable for highly acidic or alkaline solutions.
- POM: Offers good mechanical properties and is resistant to weak acids and alkalis.
- PPS: The best choice for handling strong acids and alkaline solutions due to its excellent chemical stability.
- Aluminum Alloy: Lightweight but limited in its resistance to aggressive chemicals.
- Stainless Steel: A versatile and durable option, but the compatibility will depend on the specific chemical environment.
Conclusion
Choosing the right corrosion-resistant miniature diaphragm pump depends on several factors, including the chemical compatibility of the pump's diaphragm and casing materials, flow rate, pressure requirements, and temperature resistance. Understanding the compatibility of different materials with specific acidic or alkaline media is essential for ensuring optimal performance and longevity.
For applications involving highly corrosive media, PTFE diaphragms paired with PPS or stainless steel casings offer the best solution, providing superior chemical resistance and reliable performance.
When in doubt, consult with experts who can help you select the best diaphragm pump for your unique requirements. Contact BODENFLO (info@bodenpump.com) for professional guidance on pump selection and customized solutions that meet your needs.