
Micro pump as a pump in the small size of the subdivision, with the development of science and technology, the application field is more and more extensive.
Micro pumps can be divided into micro air pumps and micro liquid pumps according to different fluids. A related article on micro air pumps can be viewed here.
The following is a discussion of miniature liquid pumps.
Common micro-liquid pumps are gear pumps, peristaltic pumps, diaphragm liquid pumps.
These three pumps are widely used in the chemical industry, medical industry, automotive industry, filling industry, printing industry, etc..
The difference between them is that the difference in structure leads to a very different shape of the design.
In terms of performance, pressure, flow rate and cost performance are the main reasons affecting the user's selection.
This article will analyze and compare these three types of pumps according to their performance, advantages and disadvantages, and cost performance, so as to better help the user to select a model.
Classification of pumps
As a kind of power equipment, a pump is a machine that conveys fluid or makes fluidly pressurized.
According to the working principle, it is divided into:
1. volumetric pump
Relying on the movement of the working parts in the process of periodically changing the volume of the pump cavity, with the role and displacement of the periodic changes in the ability to transfer to the conveyed value, so that its pressure directly to the required pressure value to achieve delivery.
According to the different ways of moving parts movement is divided into the reciprocating pump and rotary pump two types.
Reciprocating pump
It is a kind of positive displacement pump and is widely used. A reciprocating pump is a conveying machine that provides energy to the fluid directly in the form of pressure energy through the reciprocating motion of the piston.
Reciprocating pumps include:
- Piston pumps
- Plunger pumps
- Diaphragm pump
- Squeeze pump
Rotor pump
A rotor pump, also known as a colloid pump, lobe pump, triple lobe pump or universal transfer pump, etc., is a volumetric pump. It is the purpose of conveying fluid by means of the periodic transformation of multiple fixed volumes conveying units in the working chamber.
Types of rotor pumps: (the following all belong to rotor pumps)
- Screw pumps
- Liquid ring pumps
- Gear pumps
- Sliding vane pumps
- Roots pumps
- Roller pumps
- Cam Pumps
- Peristaltic pumps
2. Impeller type pump
The impeller pump is driven by the impeller to rotate the liquid at high speed and transfer the mechanical energy to the conveyed liquid.
According to the pump impeller and flow channel structure characteristics of different impeller type can be divided into.
- Centrifugal pumps
- Axial flow pumps
- Mixed-flow pumps
- Peripheral pump
3. Jet pump
It relies on the high-speed jet generated by the working fluid to induce the fluid, and then the energy of the induced fluid increases through momentum exchange.
Classification of micro pumps
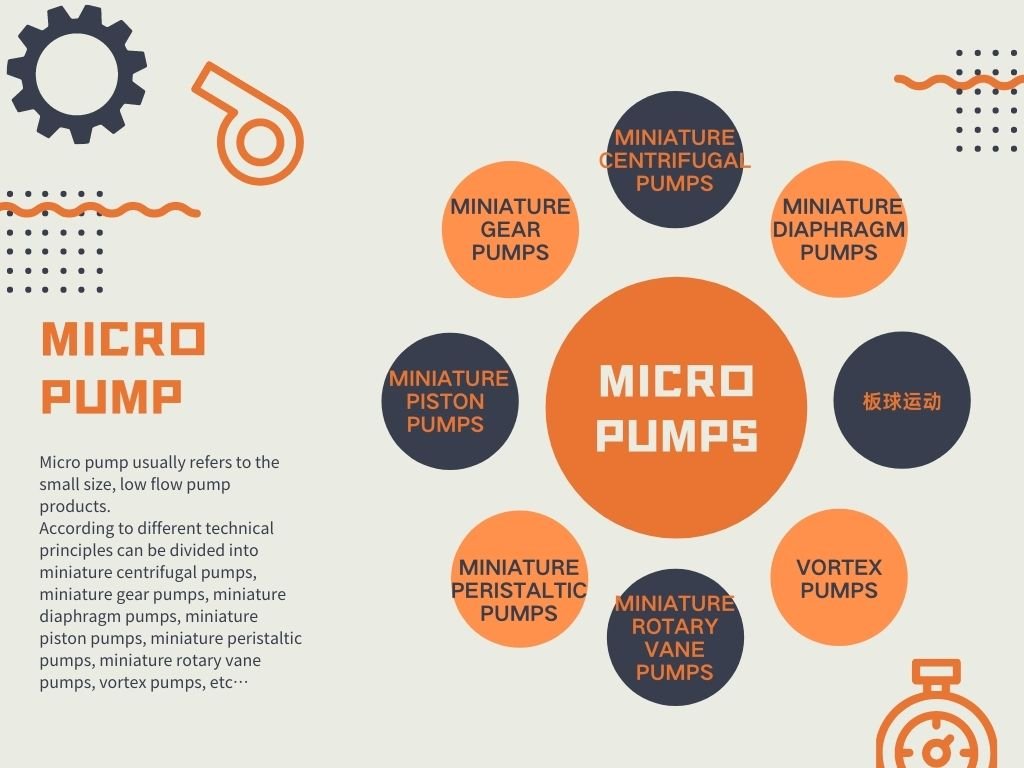
Micro pump usually refers to the small size, low flow pump products.
According to different technical principles can be divided into miniature centrifugal pumps, miniature gear pumps, miniature diaphragm pumps, miniature piston pumps, miniature peristaltic pumps, miniature rotary vane pumps, vortex pumps, etc...
- According to the driving method can be divided into direct connection, magnetic drive type.
- According to the movement mode can be divided into reciprocating and rotary type.
- According to the material can be divided into metal pumps, plastic pumps, composite pumps, etc..
- According to the temperature of the conveyed liquid, it can be divided into low temperature pump, high temperature pump and normal temperature pump.
- According to different power sources can be divided into pneumatic pumps, DC pumps (3V, 6V, 12V, 24v, 48v, etc.), servo pumps, AC pumps, inverter pumps, etc..
- Users are often accustomed to use their actual needs to name the pump, such as circulation pump, pressurization pump, sampling pump, cooling pump, urea pump, chromatography pump, flushing pump, atomization pump, etc..
With so many subdivisions, it is inevitable that the user's choice of pump brings a lot of confusion, here I am for the structure and performance characteristics of the miniature pump, combined with common applications to do some analysis and recommendations for reference when selecting a pump.
No matter what type of pump, everything changes, their role is to make the liquid to be transported by doing work, so that the liquid to be transported to produce the required flow.
Here comes the most basic parameters of pump selection: flow rate and pressure.
Generally speaking, centrifugal pumps are difficult to achieve high head (high pressure) at small flow rates, so in the need for small flow rates and high-pressure occasions, the frequency of volumetric pumps is very high.
One of the three most frequently used volumetric pumps are miniature gear pumps, peristaltic pumps, miniature diaphragm liquid pumps.
This article will analyze and compare the following three miniature pumps in terms of their ability to transport liquids, to help customers better choose the type of pump.
Micro Gear Pump VS Peristaltic Pump VS Diaphragm Liquid Pump
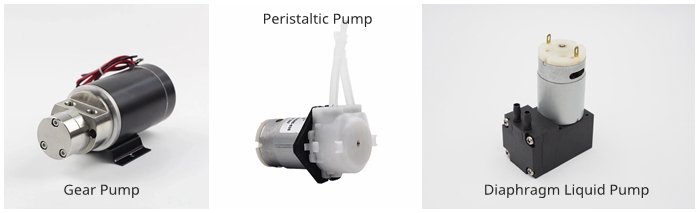
Gear Pump | Peristaltic Pump | Diaphragm Liquid Pump | |
Use generalization | Gear pumps are used when viscous fluids that do not contain solid particles need to be pumped at high pressure. Therefore, gear pumps are suitable for pumping highly viscous materials at high temperatures and are also capable of reversing the direction of pumping. | Peristaltic pumps can be considered when it is necessary to ensure that the fluid being pumped is not contaminated by external substances. This pump is ideal for clean, sterile or corrosive media. This pump also allows you to accurately dose media. | When there is a need to pump corrosive liquids, consider using a diaphragm liquid pump. This pump is small in size, has suction power, and can also be pressurized. |
working principle | A rotary pump relies on the change and movement of the working volume formed between the pump cylinder and the meshing gear to convey fluid or pressurize it. | The rollers alternately squeeze and release the pump's flexible delivery hose to pump the fluid. | Pumping of fluid by reciprocating vibration of the membrane. |
Transmission medium | Transmission of viscous oil substances (can lubricate the gears), the fluid can not have solid particles, strong acid and alkali fluids are also not allowed. | It can transmit fluids with particles, strong acids, strong bases and strong organic solvents. | Transmission of non-particulate fluids, but also strong acid and strong alkali and strong organic solvent fluids |
advantage | 1. This pump is characterized by constant flow and low noise during operation. 2. High-end gear pumps are usually reliable, compact and simple in design, so maintenance costs are not very high. | 1. peristaltic pump with shut-off valve function, no one-way check valve, no seals, no clogging or wear problems. 2. the liquid only through the peristaltic pump hose, no dead space, very clean and sanitary. 3. With self-priming function, low flow but high precision, small pulse | 1. Self-priming function (no tank to draw water), can be idle operation (water pumping, gas pumping in case of water). 2. diaphragm optional materials, corrosion resistance, high flow and pressure, maintenance-free. |
shortcoming | 1. Low-end gear pumps have leaks. 2. Not ideal for high flow use. | 1. Low flow & pressure 2. The pump also requires regular maintenance to prevent hose wear in the pump body, and the hose is the only component that needs to be replaced, with high maintenance and consumable costs. 3. Flow rate has pulses. | 1. Moderate pressure and flow rate while maintaining a small size. 2. Flow rate has pulses, but the effect is not significant. |
typical application | 1. Gear pumps are widely used in the automotive industry to lubricate all engine components. 2. They are also frequently used in plastic processing, automatic presses or in the foundry industry. | Mainly used in the chemical industry, pharmaceutical industry, medical device industry, food industry. Such as metering pumps, filling pumps. | Mainly used in the chemical industry, printing industry, cleaning industry. Such as ink pumps, self-priming pumps, chemical pumps. |
Hygienic level | ★ | ★ ★ ★ | ★ ★ |
Precision | ★ ★ | ★ ★ ★ | ★ ★ |
preservative | ★ | ★ ★ ★ | ★ ★ ★ |
Self-priming function | √ | √ | √ |
Idling | × | √ | √ |
pressure | ★ ★ ★ | ★ | ★ ★ |
flow | ★ ★ | ★ | ★ ★ |
Lift | ★ ★ ★ | ★ | ★ ★ |
Suction | ★ ★ | ★ | ★ ★ |
noise | ★ ★ | ★ | ★ |
Liquid viscosity | ★ ★ ★ | ★ ★ | ★ ★ |
pulse | ★ | ★ ★ | ★ ★ |
Consumables | × | √ | × |
Liquid and gas dual purpose | ★ | ★ ★ | ★ ★ |
efficient | ★ | ★ ★ ★ | ★ ★ |
size | ★ ★ | ★ | ★ |
cost | ★ ★ | ★ | ★ |