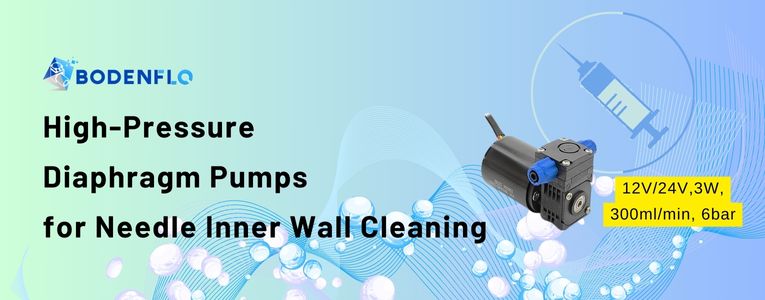
In the manufacturing and use of precision components such as needles and cannulas, residual microscopic particles and contaminants inside these narrow channels are difficult to remove thoroughly, impacting product performance and safety. This makes efficient, thorough cleaning an issue that cannot be overlooked.
High-pressure diaphragm pumps are an ideal tool specifically designed for cleaning needle inner walls. By utilizing high pressure and stable flow, they effectively remove residual particles from the inner walls, ensuring complete and safe cleaning.
Have you ever wondered how a high-pressure diaphragm pump achieves such efficient cleaning? Let’s dive into its working principles and application advantages.
What are the Features and Working Principles of High-Pressure Diaphragm Pumps?
A high-pressure diaphragm liquid pump is a pump specifically designed to generate high pressure and stable flow, using the reciprocating motion of an elastic diaphragm to create fluid pressure. This design ensures that the fluid does not come into direct contact with the mechanical moving parts of the pump, thereby preventing possible contamination, while the diaphragm's chemical resistance makes it suitable for various cleaning fluids.
The main features of a high-pressure diaphragm pump include:
- 12V/24V DC Power Supply, Low Power Consumption: These pumps are powered by 12V or 24V direct current and have a low power consumption of only 3W, making them energy-efficient and easy to integrate into various systems.
- Brushless Motor with Long Lifespan: Equipped with a brushless motor capable of running for 8,000 to 10,000 hours, ensuring long-term reliability and minimal maintenance.
- High Pressure Output: Capable of generating sufficient pressure to effectively clean the inner walls of needles and remove stubborn contaminants and residues.
- Stable Flow, Low Pulsation: The design ensures uniform and stable fluid flow with minimal pulsation, making it suitable for applications requiring precise cleaning.
- Customizable Chemical-Resistant Diaphragms: Diaphragms made of materials such as PTFE, FKM, and others can be customized to provide excellent chemical resistance, ensuring compatibility with a variety of cleaning agents.
- Oil-Free Design: Typically designed to be oil-free, ensuring no additional contaminants are introduced during the cleaning process, thus guaranteeing optimal cleanliness.
- Adaptable to Various Cleaning Fluids: High-pressure diaphragm pumps can handle a wide range of cleaning fluids, including water-based solutions, alcohol, and solvents, ensuring broad applicability for different cleaning needs.
What are the Challenges and Solutions for Needle Inner Wall Cleaning?
Due to the small diameter and long length of needle inner walls, traditional cleaning methods often struggle to ensure thorough internal cleaning. By employing the high-pressure flushing function of high-pressure diaphragm pumps, cleaning fluids can be quickly introduced into the interior of needles, using high pressure and fluid scouring to effectively remove internal residues. This is particularly suitable for:
- Medical Needle Cleaning: High-pressure water or other sterile cleaning fluids are used to completely remove contaminants inside the needles, ensuring sterility and safety during use.
- Laboratory Instrument Cleaning: In laboratory settings, the cleanliness of needle-like instruments directly affects the accuracy of experimental results. The stable and uniform pressure provided by high-pressure diaphragm pumps ensures repeatable cleaning outcomes, reducing experimental errors.
- Precision Component Cleaning: For certain precision machined parts with narrow channels, maintaining internal cleanliness is crucial. The high-pressure flushing capability of diaphragm pumps ensures the reliability of these precision components during subsequent assembly and use.
What are the Advantages of High-Pressure Diaphragm Pumps?
The advantages of high-pressure diaphragm pumps for needle inner wall cleaning include:
- Efficiency: Capable of completing high-quality cleaning in a short amount of time, significantly improving production efficiency, especially in mass production settings.
- Controllability: The adjustable pressure and flow allow optimization of the cleaning process according to the specifications and materials of different needles, ensuring the best cleaning results.
- Environmental Friendliness: The oil-free design, combined with the use of environmentally friendly cleaning agents, reduces environmental pollution and aligns with modern industry’s demand for green production.
- Long Service Life: High-pressure diaphragm pumps are typically designed for long service life, providing stable operation over extended periods, reducing the frequency of equipment replacement and maintenance, thus lowering maintenance costs for enterprises.
- Low Maintenance Requirements: Due to the oil-free design and chemical resistance, high-pressure diaphragm pumps have low maintenance needs, reducing equipment downtime and increasing overall production efficiency.
Application of BODENFLO High-Pressure Diaphragm Pumps in Needle Inner Wall Cleaning
BODENFLO offers 12/24V high-pressure diaphragm liquid pumps that are particularly suitable for needle inner wall cleaning. With a flow capacity of 300 ml/min, a maximum pressure 600 kPa, and a lifespan of up to 10,000 hours, these high-performance pumps ensure precise cleaning under high-pressure conditions, effectively removing contaminants and residues from the inner walls of needles. This significantly improves the efficiency and effectiveness of the cleaning process, making them an ideal choice for medical device manufacturers and laboratory users.
BODENFLO high-pressure diaphragm pumps excel in various application scenarios, not only for cleaning needle inner walls but also for other precision component cleaning tasks that require high-pressure, high-precision flushing. For example, in microchannels, laboratory capillaries, and precision catheters, BODENFLO’s high-pressure diaphragm pumps ensure comprehensive and consistent cleaning due to their exceptional performance.
Conclusion
High-pressure diaphragm pumps for needle inner wall cleaning provide an efficient, stable, and environmentally friendly solution for the cleaning of precision components. With high pressure, oil-free, and corrosion-resistant designs, they ensure that medical needles, laboratory instruments, and other equipment with high cleanliness requirements can achieve the desired cleaning effect. The application of high-pressure diaphragm pumps is increasingly recognized in modern manufacturing and laboratory cleaning processes, becoming an indispensable part of the industry.
In addition to applications in the medical and laboratory fields, high-pressure micro diaphragm liquid pumps have a wide range of potential uses in other industrial cleaning tasks. Whether used for cleaning precision components or maintaining a high level of cleanliness during production, high-pressure diaphragm pumps offer a reliable solution. With their high performance, reliability, and long service life, BODENFLO high-pressure diaphragm pumps have become the ideal choice for many industry users.
If you have more requirements or technical questions regarding high-pressure diaphragm pumps for needle inner wall cleaning, feel free to contact us (info@bodenpump.com) for in-depth discussions. We are committed to providing high-quality products and professional technical support to meet your various needs in the field of precision cleaning.