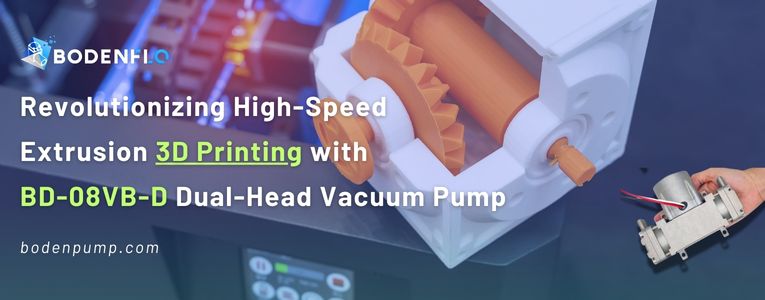
In the rapidly evolving world of 3D printing, speed and precision are paramount. At BODENFLO, we are pushing the boundaries of what's possible in additive manufacturing with our cutting-edge BD-08VB-D Dual-Head Vacuum Pump. This powerful component is transforming how High-Speed Extrusion (HSE) 3D printers operate, making them faster, more precise, and more efficient than ever before.
The integration of our BD-08VB-D vacuum pump into HSE 3D printers marks a significant leap forward in the industry. By providing enhanced suction and precision placement, this pump optimizes every cycle of the printing process, ensuring flawless operation and superior final products.
The demand for faster production times without sacrificing quality is a constant challenge in manufacturing. Our dual-head vacuum compressor pump addresses this by enabling quicker and more accurate movements within 3D printers, which is essential for achieving high-quality prints in reduced times.
What is Industrial High-Speed Extrusion 3D Printing?
Industrial High-Speed Extrusion (HSE) 3D Printing refers to a cutting-edge additive manufacturing technology designed to significantly increase the speed of the 3D printing process while maintaining or enhancing the precision and quality of the output. This technology is particularly adapted for industrial applications where the demand for rapid production and high throughput is critical.
Technical Challenges of Vacuum Pumps in Industrial 3D Printers
Integrating vacuum pumps into industrial high-speed extrusion 3D printers presents several technical challenges crucial for ensuring operational efficiency and product quality:
- Maintaining Precision Under High Speeds: High-speed printing demands rapid responses from vacuum systems to manage material handling without errors. Achieving precision requires robust control systems capable of rapid adjustments to vacuum levels, ensuring consistent material placement even at high speeds.
- Ensuring Vacuum Stability: Consistent vacuum strength is essential to handle varied materials and complex shapes without interruptions. Advanced airflow management and responsive control mechanisms are needed to maintain stable vacuum conditions, adapting quickly to changes in printing dynamics.
- Minimizing Noise and Vibration: High operational speeds can increase noise and vibrations, which may interfere with the precision of the printing process. Vacuum pumps designed for these environments typically incorporate specialized mounts and noise-reduction technologies to operate quietly and without disruptive vibrations.
- Managing Heat Accumulation: The rapid operation of vacuum pumps generates significant heat, which can affect performance and longevity if not properly managed. Effective thermal management strategies, such as integrated cooling systems or heat-resistant materials, are critical to prevent overheating and maintain consistent performance.
- Durability and Low Maintenance: Industrial 3D printers require vacuum pumps that can withstand long operation periods under demanding conditions without frequent maintenance. Durable materials and designs that minimize wear are essential, along with systems that allow for easy maintenance to avoid prolonged downtime.
These challenges highlight the need for well-designed vacuum systems that can meet the rigorous demands of high-speed extrusion 3D printing. While specific products like the BD-08VB-D Dual-Head Vacuum Pump may be part of broader solutions, the focus remains on the overall capability of vacuum technology to support advanced industrial applications efficiently.
Why is the 70L BD-08VB-D Dual-Head Vacuum Pump Vital for 3D Printers?
The BD-08VB-D Dual-Head Vacuum Pump from BODENFLO is an integral component in revolutionizing the capabilities of High-Speed Extrusion (HSE) 3D printers. Its design and performance directly address the critical needs of modern industrial additive manufacturing processes. Here are the reasons why this vacuum pump is essential for any HSE 3D printing setup:
- Enhanced Precision and Control: The 70L BD-08VB-D vacuum pump delivers unmatched control over material handling, crucial for the HSE 3D printing industry. With its ability to maintain consistent suction throughout the printing process, the pump ensures materials are deposited with exceptional accuracy. This precision is vital when producing complex and intricate 3D models, where even minor inaccuracies can significantly impact the quality and integrity of the final products.
- Increased Production Speed: Incorporating the BD-08VB-D into HSE 3D printers dramatically enhances the efficiency of the printing process. The pump's rapid response time and robust suction reduce the time needed for material handling, thus speeding up the entire printing operation. This efficiency is especially beneficial in industrial environments where reducing production time is directly linked to cost savings and increased output.
- Reliability and Durability: The BD-08VB-D is built to withstand the rigorous conditions of continuous industrial use. Its durable design reduces wear and extends the pump's life, minimizing the maintenance required and ensuring consistent performance. This reliability is crucial for manufacturers who rely on continuous and uninterrupted operation to meet production demands.
- Scalability and Flexibility: This dual-head vacuum pump is designed to be adaptable, meeting various operational demands without the need for extensive modifications. Its compact size and the ability to function in either continuous or intermittent modes make it suitable for diverse 3D printing applications, from small-scale prototypes to large-scale production. This flexibility allows for quick adjustments to production scales and material types, enhancing the overall efficiency of the manufacturing process.
Key Features of the BD-08VB-D Dual-Head Vacuum Pump
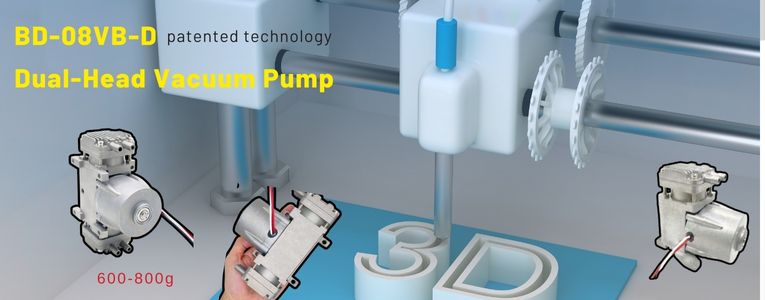
At BODENFLO, our commitment to innovation and quality is exemplified in the design of the BD-08VB-D Dual-Head Vacuum Pump. This model is specifically engineered to meet the demanding needs of industrial applications, including High-Speed Extrusion (HSE) 3D printing. Here are the distinctive features of the BD-08VB-D that set it apart in the market:
High Performance and Efficiency
- Powerful Suction: The BD-08VB-D delivers a maximum vacuum of -85 kpa, ensuring efficient material handling and precise placement essential for complex manufacturing processes.
- High Flow Rate: With a substantial flow rate of 70L/min, this pump can handle high-volume tasks quickly and effectively, maximizing productivity and reducing downtime in industrial settings.
Robust and Reliable Motor
- 24V DC Brushless Motor: The use of a high-torque brushless motor guarantees not only longevity but also reliable performance under continuous or intermittent operating conditions. This motor type is ideal for scenarios requiring a high startup load, ensuring the pump operates efficiently from the start.
- Low Current Draw: Operating at less than 4.5A, the BD-08VB-D is energy-efficient, reducing overall electricity consumption and operating costs for businesses.
Lightweight and Durable Construction
- Compact and Lightweight: Weighing just 806 grams and with compact dimensions of 131 x 64 x 106.5 mm, the BD-08VB-D is easy to integrate into existing systems without requiring substantial modifications.
- Aluminum Alloy Housing: The use of aluminum alloy for the pump’s body not only provides robustness but also ensures heat dissipation, contributing to the pump’s ability to operate under various environmental conditions without overheating.
- High-Pressure and Temperature Resistance: The components, including the high-pressure resistant valves and heat-resistant rubber, are selected to withstand challenging industrial environments, ensuring durability and reducing the need for frequent replacements.
Designed for Versatility
- Flexible Application: Whether used in continuous or intermittent modes, the BD-08VB-D adapts to different operational requirements, offering manufacturers the flexibility needed in dynamic production environments.
- Self-Developed with Patent Technology: As a testament to our focus on innovation, the BD-08VB-D is developed in-house, incorporating proprietary technologies that enhance its performance and reliability.
The BD-08VB-D Double Head Vacuum Pump is more than just a component; it’s a critical tool designed to enhance the capabilities of modern industrial machinery, including 3D printers. Its ability to deliver consistent, reliable performance while managing significant volumes of work effortlessly makes it a valuable asset in any high-demand manufacturing setting.
Market Trends of Miniature Vacuum Pumps in Industrial 3D Printing
As the demand for faster, more efficient production continues to rise in various sectors, the industrial 3D printing industry is undergoing significant transformations. Miniature vacuum pumps, like our BD-08VB-D Dual-Head Vacuum Pump, are at the forefront of this revolution, enabling advancements in High-Speed Extrusion (HSE) 3D printing technologies. This segment explores the current market trends that highlight the growing integration of miniature vacuum pumps into industrial 3D printing operations.
Growing Demand for Speed and Efficiency
In today’s market, there is a pronounced shift towards increasing the speed of 3D printing processes without compromising the quality of outputs. This trend is largely driven by sectors such as aerospace, automotive, and healthcare, where production efficiency directly correlates with competitive advantage and cost management. Miniature vacuum pumps are critical in meeting these requirements due to their ability to facilitate quicker material handling and positioning with high precision.
Advancements in Material Compatibility
The expansion of material options in 3D printing—ranging from polymers to advanced composites—necessitates the use of adaptable and robust vacuum systems. Miniature vacuum pumps are being developed to handle a broader range of materials, which enhances the versatility of 3D printing machines. This adaptability allows manufacturers to explore new applications and innovate within their respective fields, driving further adoption of HSE 3D printing technologies.
Integration with Smart Factory Solutions
Another significant trend is the integration of vacuum pumps with smart factory environments, where IoT (Internet of Things) technologies play a pivotal role. Advanced sensors and control systems embedded within miniature vacuum pumps enable real-time monitoring and adjustments during the printing process, leading to smarter, more connected manufacturing workflows. This integration supports the broader movement towards Industry 4.0, where automation and data exchange are key components.
Focus on Sustainability
Environmental considerations are increasingly influencing the design and operation of industrial equipment, including 3D printers. Energy-efficient miniature vacuum pumps are becoming more prevalent, as they help reduce the overall energy consumption of 3D printing operations. Additionally, the ability of these pumps to operate with precision minimizes waste material, further supporting sustainable manufacturing practices.
Economic Outlook
The economic landscape for miniature vacuum pumps in the industrial 3D printing market is promising. With the continuous growth of 3D printing applications across industries, the demand for reliable and efficient vacuum pumps is expected to rise. Companies that innovate in this space, enhancing their products to offer greater efficiency, reliability, and integration capabilities, are well-positioned to capitalize on this expanding market.
Conclusion
The integration of miniature vacuum pumps like the BD-08VB-D into industrial 3D printers is not just enhancing the capabilities of these machines; it's reshaping the manufacturing landscape. By driving advancements in speed, efficiency, and material versatility, these pumps are helping businesses meet the challenges of modern manufacturing demands. At BODENFLO, we remain committed to developing vacuum solutions that support the growth and innovation of our customers in the industrial 3D printing sector.
For more insights into how our vacuum technologies can transform your production processes, visit our website or reach out directly at info@bodenpump.com. Our team is ready to assist you in integrating state-of-the-art vacuum solutions that align with your manufacturing goals and industry trends.