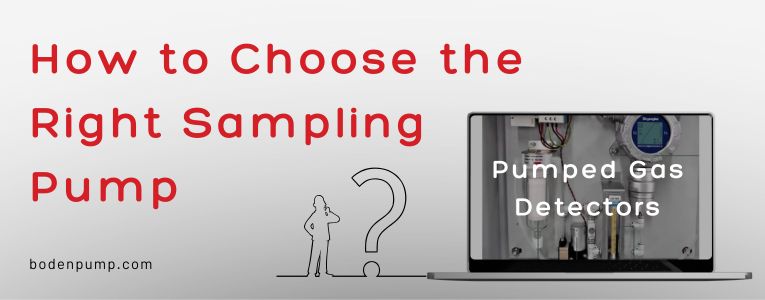
Are you facing challenges with the performance of your pumped gas detector? Many users struggle with issues like inaccurate sampling, slow response times, or inefficient gas flow, which can compromise results and affect overall efficiency. Choosing the right sampling pump is the solution to these problems, ensuring improved accuracy, faster detection, and smoother integration with your gas detector.
Selecting the right sampling pump for your pumped gas detector is crucial for achieving optimal performance. Key considerations include matching the flow rate and pressure requirements, ensuring gas compatibility, and selecting a pump that minimizes noise and vibration. With the correct sampling pump, you can enhance the stability and efficiency of your gas detection system, ensuring precise and reliable results.
To make the best choice, you need to evaluate various factors in detail. Let’s dive into how to find the perfect sampling pump for your needs.
Identifying the Issue: Why Is Choosing the Right Sampling Pump So Important?
In the field of gas monitoring, sampling pumps not only need to provide stable and accurate gas sampling, but they also need to ensure compatibility with the gas detector. Different applications demand different requirements for sampling pumps, and improper selection can lead to the following issues:
- Decreased Sampling Accuracy: If the sampling pump’s flow rate or pressure is unstable, it will affect the accuracy of the gas sample.
- Delayed Response Time: An unsuitable pump can prolong the sampling process, leading to slower response times for the gas detector.
- System Incompatibility: If the pump design doesn’t match the gas detector, issues such as difficult installation, gas flow disruptions, or equipment failure can arise.
To avoid these problems, selecting the appropriate sampling pump is a crucial step in optimizing the performance of a pumped gas detector.
Key Performance Factors: How to Evaluate the Suitability of a Sampling Pump?
When selecting a sampling pump, several performance factors should be taken into consideration:
Flow Rate and Pressure Requirements
Gas detectors have specific flow rate and pressure requirements, and the sampling pump must match these parameters.
- Flow Rate: The sampling pump needs to have a sufficiently high flow rate to collect enough gas samples quickly. Flow rates are typically measured in L/min, with common ranges being 10–50 L/min. If the flow rate is too high, the gas sample may be collected too quickly, affecting its representativeness. Conversely, a flow rate that is too low may result in inadequate sampling, thus affecting measurement accuracy.
- Pressure: The sampling pump’s pressure range should be compatible with the gas detector’s design to ensure the smooth flow of gas samples into the detector. Generally, the sampling pump needs to provide adequate vacuum pressure for sample collection, but too much vacuum pressure may cause leaks or damage the pump.
Gas Compatibility
Different gases have varying chemical properties, such as corrosiveness, flammability, and toxicity. The sampling pump must be compatible with the specific type of gas being monitored to avoid material degradation or leaks.
- Material Selection: For corrosive or high-temperature gases, the sampling pump typically needs to be made from corrosion-resistant materials like stainless steel, PTFE, or aluminum alloy. For flammable or toxic gases, the pump must be designed with safety features to ensure fire and explosion prevention to protect both operators and the environment.
- Gas Concentration: The pump’s design must also account for the gas concentration range, especially when high-concentration gases are being sampled. The pump should be constructed with materials and features that can withstand high concentrations without compromising its integrity.
Pump Noise and Vibration Control
Noise and vibration are potential issues that can arise during the operation of sampling pumps. Excessive noise and vibration not only affect the long-term reliability of the equipment but may also disrupt the working environment, especially in sensitive settings such as laboratories or medical facilities.
To minimize noise and vibration, the design of the sampling pump should focus on material selection, structural optimization, and motor configuration. Opting for a low-noise design ensures quieter operation, improving user comfort and contributing to a better working environment.
Pump Efficiency and Longevity
The energy efficiency and longevity of the sampling pump are crucial for evaluating its long-term operating costs and stability. High-efficiency pumps reduce operating costs, while durable pumps minimize the need for frequent maintenance and replacement.
- Energy Efficiency: An energy-efficient sampling pump delivers stable performance while consuming less electricity. Selecting an energy-efficient pump helps lower long-term operating costs, especially in large-scale gas monitoring applications.
- Longevity: The durability and lifespan of the sampling pump are greatly influenced by its design and material choices. High-quality materials and precision manufacturing ensure that the sampling pump remains reliable and durable throughout its operational life.
Solutions: How to Choose the Right Sampling Pump Based on Application Requirements?
The right sampling pump should be chosen according to the specific gas monitoring needs. Here are some common applications and the recommended sampling pump types:
Environmental Gas Monitoring
Environmental gas monitoring typically involves the detection of atmospheric gases such as CO2, nitrogen, and oxygen. To ensure high accuracy and stability, it is recommended to select a sampling pump with a flow rate range of 20–50 L/min and stable negative pressure. The pump should be made of corrosion-resistant materials such as stainless steel or PTFE.
Industrial Gas Detection
Industrial gas detection involves a wide range of gases, including toxic and hazardous substances. The sampling pump must have strong chemical resistance and high-temperature capabilities. It is recommended to use pumps with filtration features to protect the pump from harmful gases. A flow rate range of 10–30 L/min and a pressure range of 1–5 bar are suitable for these applications.
Medical Applications
In the medical field, especially for monitoring patient respiratory gases, the sampling pump needs to be highly precise and stable. A low-noise, low-vibration, and contamination-free sampling pump is essential for these applications. The flow rate typically ranges from 5–10 L/min, and the pump must meet medical standards for materials and operation.
Laboratory Applications
Laboratory gas analysis requires highly accurate gas sampling systems. The sampling pump must provide stable flow rates and pressures to ensure precise analysis. A low-noise, low-maintenance pump is recommended for laboratory environments. Flow rates in the range of 10–20 L/min are generally suitable for this application.
Implementation and Verification: Ensuring Optimal Integration of the Sampling Pump with the Gas Detector
After selecting the appropriate sampling pump, customers should conduct thorough system testing to ensure proper integration with the gas detector. The testing process should include:
- Flow Rate and Pressure Testing: Verify that the sampling pump’s flow rate and pressure meet the gas detector’s requirements.
- Stability Testing: Test the gas sampling system under various environmental conditions (e.g., temperature and humidity variations) to ensure stable operation.
- Long-Term Operational Testing: Conduct extended operational testing to assess the durability and reliability of the pump under continuous use.
Conclusion: Selecting the Right Sampling Pump to Enhance Pumped Gas Detector Performance
Choosing the right sampling pump is vital to optimizing the performance of a pumped gas detector. By carefully evaluating factors such as flow rate, pressure, gas compatibility, noise control, and system compatibility, customers can ensure their selected sampling pump integrates seamlessly with the gas detector. This results in improved sampling accuracy, faster response times, and longer operational lifespans. Proper selection and optimization of the sampling pump will significantly enhance the overall performance of the gas detector, ensuring it meets the high standards required for various industrial, environmental, medical, and laboratory applications.
Ready to enhance your pumped gas detector performance? Contact us today (info@bodenpump.com) to find the perfect sampling pump tailored to your needs!