
Despite the fact that both Steppers and Dc Motors use direct current, their designs, working principles, and applications are different.
With so many factors to consider, it's no surprise that many people still find it challenging to locate an ideal motor for their intended applications. As a result, we've put up a guide to assist you in the buying process, so you can choose an ideal motor for your project.
In this article, we will discuss the applications and advantages of stepper motors and Dc motors. Also, we will take a look at the differences between steppers and Dc motors and various factors to consider when choosing your motor type.
What Is A Stepper Motor?

AC Stepper motors are electromechanical device that transforms electrical energy into mechanical energy. They are synchronous, brushless electric motors capable of dividing a whole revolution into different stages. As long as the equipment is correctly designed for the operation, the orientation of the motor can be regulated precisely without the use of a feedback device.
The rotor contains six poles, whereas the stator has eight poles. When energy is applied to the motor, it employs a magnet to cause the motor shaft to move a certain distance. In achieving one complete rotation, the rotor always needs 20 pulsations of power to move the 20 steps. Different categories of stepper motors include rid-synchronous, permanent-magnet, and variable-reluctance stepper motors.
Stepper Motor Applications
Healthcare applications – This motor is always integrated into medical samplers, respirators, scanners, liquid pumps, and diagnostic and screening apparatus.
Industrial apparatus – A stepper motor is used in automobile gauges, electric vehicles, as well as automated manufacturing systems, and machine tooling.
Security – These motors are used in surveillance devices such as security cameras.
Homebased electronics – Stepper motor is used in cameras to automate the focusing and zooming capabilities.
What Are The Advantages Of Stepper Motors?
Maximum torque
At a standstill, stepper motors still offer high torque while the angle of rotation of the motors is proportional to the incoming electrical pulses. Stepper motors provide precise position control, superb speed, and repeat the movement.
Reliable
Stepper motors are highly reliable since they do not use contact brushes. This minimizes possible mechanical failures and ensures the durability of the motor. Also, this reduces the cost of maintenance.
Applicability
Stepper motors are applicable in a number of sectors. Their speed corresponds to the frequency of pulse inputs – they always attain high rotational speeds.
Inexpensive
These devices are affordable and readily available. They call for less maintenance compared to DC and servo motors. They do not require torque feedback, thus simple and less costly to produce.
Safe
Unlike other motors that get damaged easily when overloaded, stepper motors are enduring. They will still provide a full torque even when stationary.
What Affects Stepper Motor Efficiency?
Resonance
This is when the motor tends to overshoot the final resting point when it completes every single step. Without regular maintenance, this can always cause stalling.
No feedback
A stepper motor does not use a feedback loop. Feedback allows the machine to make alerts when things are going wrong. A stepper motor will have to rely on other systems such as computers and hall effect sensors for this.
Magnetostriction
This is when magnetostriction distorts the iron and pulls the rotor and stator teeth in the direction of each other, producing electromagnetic noise due to the air gap.
High speed
The efficiency of stepper motors fluctuates with an increase in the operational speed. At a higher speed, they are unsuitable for a heavy load since the torque decreases as it moves fast.
Low speed
A Stepper motor offers maximum torque when running at a low speed. This makes them suitable for low speed applications.
What Is A DC Motor?
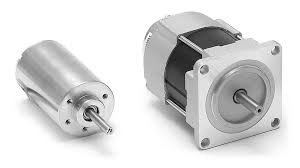
DC motors are machines that transform electric power into rotary mechanical power through the interactions of a conductor and magnetic field. They are controllable, dependable, and inexpensive to buy and install. They are available in hundreds of different ratings.
DC motor is best suited for applications demanding consistent torque over the motor's maximum speed. Fast and continuous rotation motors are mostly employed in operations that use high rotation per minute, such as computer fans for conditioning or automobile wheels operated by radio. Categories of Dc motors include;
Brushed DC motors
A Brushed DC motor is an electric motor that depends on the brush for contact with the stator. They are just DC motors with permanent magnets and a revolving rotor. They are used today in electric vehicles systems to power car windows and steering wheel adjustments.
Brushless DC motors
Brushless motors operate by changing the direction of the windings within the motor. Generally, they are inside-out brushed motors that lack brushes. In brushless motors, the permanent magnet is always attached to the armature of the motor, whereas the electromagnet is attached to the stator. The electromagnet’s energy in the stator is regulated by electronic speed controllers, allowing the rotor to rotate. Like the stepper motor and the Servo motor, these motors produce little to no electromagnetic noise.
Advantages Of Dc Motors
Excellent speed control
DC motors have much better control of speed compared to AC motors. This is obtained by alternating the armature and field voltage hence having a speed range that varies widely; DC motors tend to be precise, with constant speed, thus the best for most appliances.
Constant maintenance of high torque
A DC motor can keep up the maximum torque constant. This makes it suitable for heavier loads such as industrial machinery and stocky plants. Also, it is employed in applications requiring constant torque throughout the operation for geared systems.
Heavy load applications
The motor's compact design and greater continuous torque make it suitable for loading equipment in industrial motors.
Uses Of DC Motors
Some of the applications of various types of dc current motors include;
A series DC motor is employed when a strong starting torque is necessary, and speed fluctuations are possible. For instance, a series motor is employed in traction systems, air compressors, cranes, sewing machines, and vacuum cleaners.
The Dc shunt motor is employed in situations where a consistent speed is necessary, and the starting settings are not harsh. DC shunt motors are used in a wide range of applications such as lathe systems, centrifugal pump, blower machines, lifts, weaving machines, conveyors, and spinning systems.
A compound dc motor is employed when a large starting torque, as well as a relatively consistent speed, is needed. They are used in a wide range of applications, including presses, shear machines, conveyors, lifts, rolling mills, and heavy excavators.
Miniature DC devices with fractional kilowatt capacities are mostly employed as controllers in tech machines for speed detection and servo motors for locating and monitoring.
What Are The Main Differences Between Stepper And Dc Motors?
The main differences between Stepper Motor and Direct Current (DC) Motor are determined by the brushes, their motion, the displacement, nature of the operating loop, the motor's response time, and the effect of overloading. They differ in the following ways;
Control mechanism
A Stepper motor is easily controlled by a microprocessor and a controller system, and therefore they are often used in microprocessor-based control systems. Dc motors, on the other hand, demand an input voltage for their leads to operate.
Loop systems
Stepper motors operate in an open-loop while the Direct current motor tends to work in a closed-loop system. An open-loop system stepper motor tends to run at maximum speed when its load capacity is not exceeded. They can make precise moves without feedback altering the motor position. Closed-loop DC systems offer secondary verification and performance, such as automatic position feedback. Closed loops are better equipped to handle any system disturbance or change their situation.
Rotation
The stepper motor increases its movements continuously; its resolution is limited by the size of the step. DC motor displaces continuously and can be accurately controlled and positioned. On the other hand, the rotation speed of stepper motors is proportional to the input pulse frequency. Stepper motors have a high torque in the low speed range and a reduced torque in the high-speed range, resulting in a loss of step.
Feedback
DC motors are closed looped systems. This means they give feedback at every complete phase, thus allowing a faster response time than a stepper motor.
Damage control
When overloaded, stepper motors can slip up and cause much damage before detection. DC motors have relays and overloads that protect devices from damage during overloading.
Application
Stepper motors are often used in CNC systems, 3D printer, X-ray imaging devices, and cameras. DC motors, on the other hand, are used in mobile vibrators, hand tools, conveyors, and other low-cost operations that require long-term voltage output.
Summary
While this brief review of the features and functionalities of stepper motors and dc motors can be enough when choosing the right motor for your application, always consider the complete information in every motor's product specification to guarantee the efficiency and durability of your motor system.
BODENFLO miniature DC motor pumps are all made with DC motors, which have the advantages of low voltage, low power consumption, low current, and small size. Our miniature DC motor pump for air and vacuum is lightweight and compact, widely used in medical and health, beauty and body, small appliances.
- Common DC pump voltages are: 3V, 3.7V, 6V, 9V, 12V, 24V.
- Common DC pump power: between 1 and 50W
For more details on our product range or to request specifications that match your requirements, please contact us at info@bodenpump.com. Let BODENFLO empower your projects with high-performance and reliable solutions.